#04
夢の素材 – 環境負荷の軽減にも効果を発揮する炭素繊維
“夢の素材”といわれる炭素繊維。航空機や風力タービン、自動車などに使用され、軽くて強いことが特長です。最新技術で進化し続けるこの素材の生産とリサイクルは、環境保全にも役立ちます。
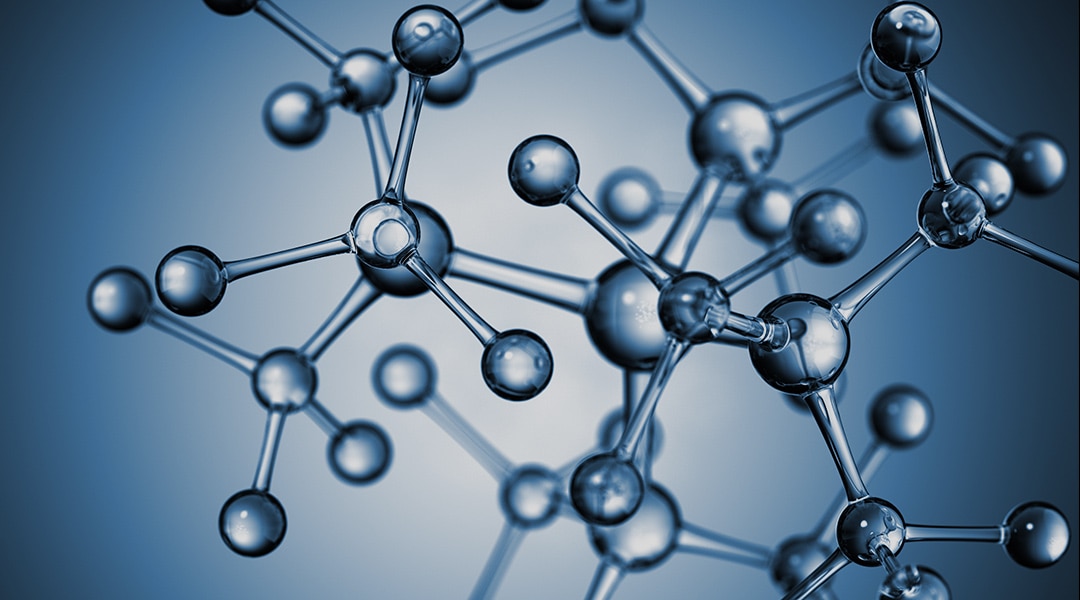
機能材料の時代が到来して以来、炭素繊維は長く市場の主役を務めてきました。軽くて強いこの素材は、鉛筆と同じグラファイト構造を持つ炭素原子の束によって成り立っています。鉄の重さの1/4、しかし強度はその10倍もあります。航空業界では航空機の尾翼にこの素材が使われており、エアバスA310やボーイング787ドリームライナーの場合は機体の各所に採り入れられています。
炭素繊維のボディは軽いため、推進力となる燃料を削減することができます。当然CO2の排出も少なくなります。しかし、このまま現状に満足しているわけにはいきません。低炭素社会の実現に向けEUは、2030年までに運輸産業に対し45%のCO2排出削減を課する方針です。
この流れは再生可能エネルギーを用いた電気自動車(EV)の開発を後押ししていますが、一般車のさらなる軽量化と低燃費化にも拍車がかかっています。新興国の旺盛な需要が世界の自動車販売を押し上げているからです。
航空業界では2013年以来、国際線の乗客定員数が年間で5%から8%増え続けており、それに応じて航空機の機体が大きくなっています。これはより重い重量を意味し、ここでも低燃費化は避けられません。そしてさらに環境のためのCO2排出削減という難問が加わります。
産業界に広まる活用事例
炭素繊維は、グラファイト構造を持つ炭素原子が集まった直径5ミクロンから10ミクロンの繊維で、その太さはちょうど人間の髪の1/10ほどになります。エポキシ樹脂と合わせて熱硬化させることで機能的な複合材を作ることができます。
高機能炭素繊維の生産は、1960年代に日本の主導ではじまりました。自転車、F1マシン、風力タービン、ノートパソコンの筐体など、現在ではその複合材がさまざまな製品分野に広がっています。すでに高い強度を持っていますが、炭素繊維のポテンシャルはこんなものではないと専門家は語ります。
強固な開発基盤と高品質製品
東レは高機能炭素繊維の開発に積極的で、1970年代から世界の研究開発を牽引してきました。近年では宇宙ロケット、人工衛星、航空機に用いられる素材を生みだしています。航空宇宙産業では過酷な環境に耐えうる最高レベルの品質が求められますが、新開発のT1100Gはまさにその代表といえます。ナノレベルの加工による最新の炭素化技術が用いられており、大きな張力や圧縮に耐え、侵食や変形、疲労にも優れた強さを発揮します。
自動車業界でも電気自動車に炭素繊維が用いられていますが、東レが開発したコンセプトカー「“TEEWAVE”AR1」は、炭素繊維のボンネット、ダッシュボード、ルーフを持ち、ショックアブソーバーには高剛性で衝撃安全性の高い炭素繊維複合材が用いられています。軽量化も特長のひとつで、市販の電気自動車の1/3の重量を実現。これによりCO2排出を9%抑えることができます。
未来に向け成長
炭素繊維にはまだ研究課題も多く残されていますが、リサイクルがそのひとつ。しかし、最近では少しずつ成果が現れてきています。たとえば、東レは炭素繊維廃棄物を焼却する際に排出されるガスを抽出し、さらに再利用する技術を豊田通商と共同で開発しました。
もうひとつの課題は生産コストです。かつて1ポンドあたり100ドルだった生産コストは現在10ドルにまで下がりましたが、それでもまだ割高と考えられています。2015年に60,000トンだった世界の炭素繊維消費量は2025年までに150,000トンに倍増する見込みで、廃棄物のリサイクルがうまく軌道に乗れば供給コストが下がり、炭素繊維の普及はさらに進むことでしょう。
“夢の素材”はいま成長の時を迎えています。風力発電のタービンや自動車、航空機への活用を足がかりに、脱炭素社会を支える存在になることは間違いありません。